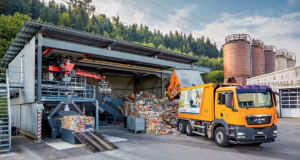
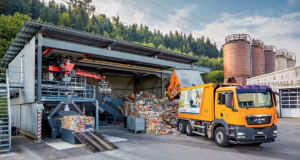
Waste and Recycling Centre Ibach, City of Lucerne, Switzerland
Operating costs of prime importance
A new baling press is now in operation at Waste and Recycling Centre Ibach near Lucerne. Operational costs played an important role in the purchase decision. Hunkeler Systeme AG’s control concept was an equally convincing argument.
The Head of Department, Centre Services, Heinz Zurkirchen is pleased for a very good reason; a new baling press went into operation at the city of Lucerne’s Waste and Recycling Centre Ibach at the end of July. Hunkeler Systeme AG planned and implemented the system. In the first two months, over 400 tons of carton were compressed into bales. This is the equivalent of a fifth of the annually processed volume. The material was collected from all over the city of Lucerne in rubbish collection vehicles and transported to the Waste and Recycling Centre.
Energy efficiency is also an important criteria
When investing in the new baling press, Heinz Zurkirchen and his colleagues were not looking for the cheapest system available. The project team wanted reliability and a high service standard from their supplier. They also wanted a tailor-made system from one individual supplier. Hunkeler Systeme AG could meet these requirements.
Heinz Zurkirchen cites operating costs as an important factor. The system from Wikon was especially persuasive when it came to energy efficiency, he noted. The control system developed by Hunkeler Systeme AG regulates the energy requirements via a frequency converter. The baling press motors only start up when there is material to be compressed. This keeps the cost per ton for compressed cardboard to a relatively low level.
‘We are working more efficiently with the new baling press’, says Heinz Zurkirchen. Compared to the previous system, this has up to 50% more performance. The press can process seven to eight tons an hour.
The rapid workflow is assisted by standardised bale sizing: at 1.8 to two metres, they are as wide as the towing vehicles. Previously, the narrower bales had to be loaded from both sides of the vehicle. Now loading takes place on one side only. It is not only faster, as Heinz Zurkirchen explains, but the transport loading is also more stable. The compressed cardboard then goes to the Model AG company in Niedergösgen, where it is used for the production of corrugated cardboard.
Teamwork with many qualities
‘We experienced working with Hunkeler Systeme AG as an enjoyable partnership. The project leader kept us up to date and the fitters worked quickly. The new press had to be installed in the same location as the previous system. Thanks to a well-organised schedule, everything was successfully carried out and the new press went into operation on time.’
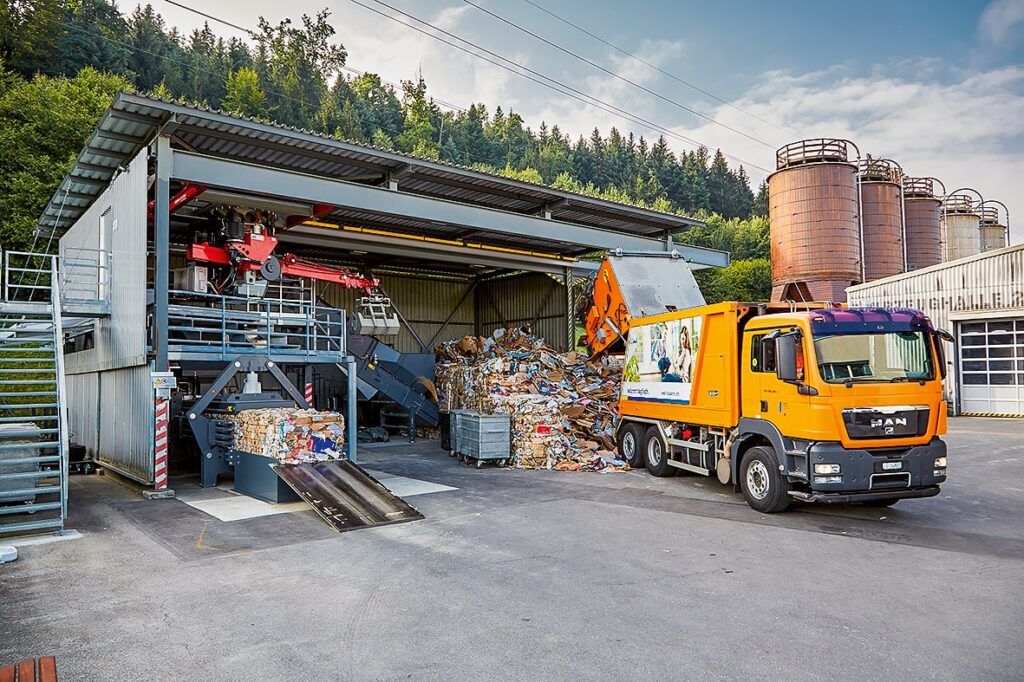
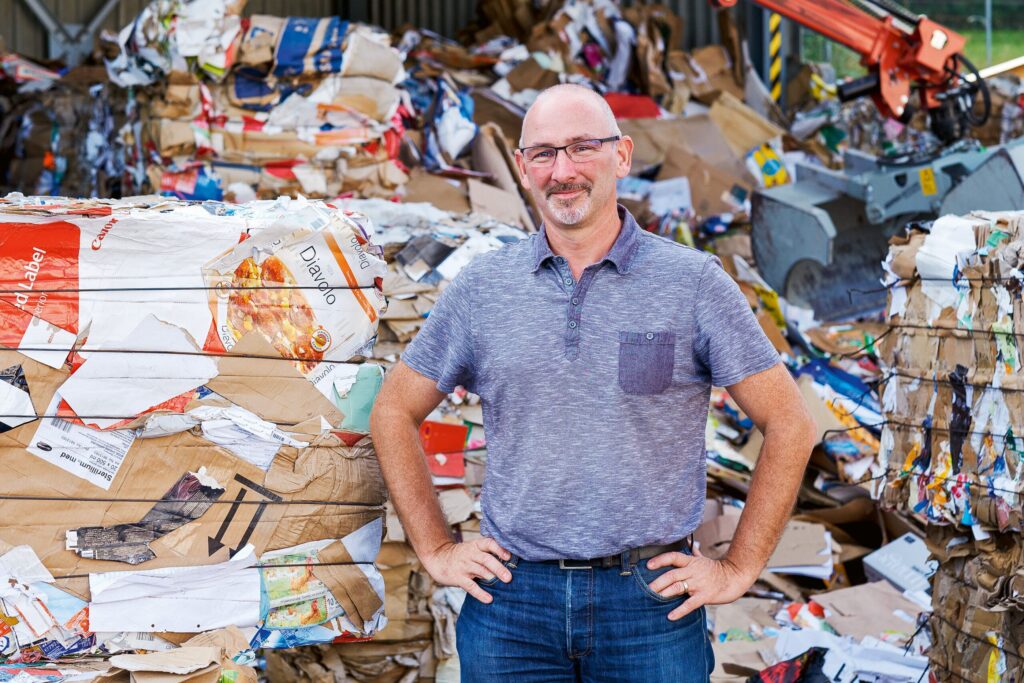