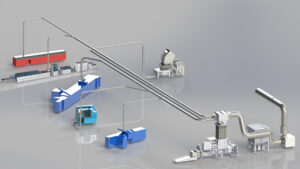
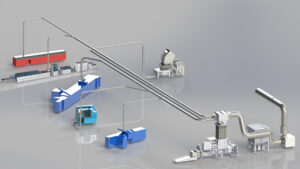
These are advantages of a waste extraction system
Waste extraction systems are designed to collect residual materials directly where they occur. These systems take a holistic approach. They are designed for integration into packaging and production plants. Typical applications are in trade and industry. Extraction systems process the waste as far as possible automatically and prepare it for disposal.
In practice, the use of such systems offers numerous advantages. Companies benefit from systems of this type through automatic separation of waste, higher productivity and other features. Individually configurable systems adapt to a wide variety of environments.
These are the functions offered by a waste extraction system
Extraction systems serve several purposes. The main tasks are to clean the air in the processing area and to separate waste materials. The extraction systems achieve these goals using different methods. The decisive factor is the type of material or packaging material being processed. The type of waste is recorded at the production machine. Then the actual process of waste extraction begins.
These are some of the functions that modern extraction systems have:
- filtering the exhaust air
- separation of air and material
- transport with negative pressure
- shredding and chipping in different variants
- compaction of the waste
Separation, filtration and separation
Part of the exhaust system is a system for separation of different materials. In the component, sorting out of the coarse materials takes place, if necessary. Air containing dust passes from here into the filter system. The coarse materials, on the other hand, are screened out by the separator and transported separately for further waste processing. Separation of different materials is also possible here.
The air filter system is a separate component. In it, filtering of the air takes place, fine particles remain in the filter. Hunkeler’s systems filter so precisely that it is possible to return the air to the hall afterwards. If desired, it can be discharged to the outside. The filtered air contains as less as 0.1 mg of dust particles per cubic meter of air.
Waste shredding and chopping
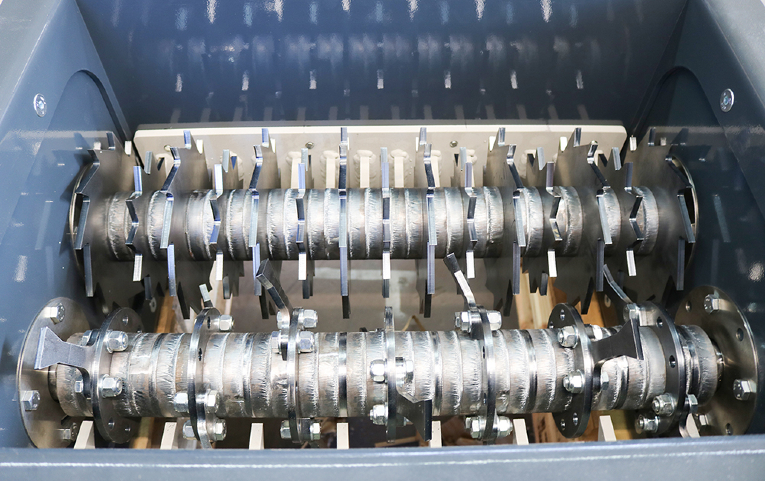
Especially in the case of coarse waste, it makes sense to process it mechanically before final disposal. This applies, for example, to cardboard, plastics and also metal parts. Different shredders, chippers and shredders make it possible to select the appropriate process for each type of waste. This significantly reduces the volume of waste.
From Hunkeler you can get pipe shredders and rotary shredders for die-cut machines. Chipper fans or horizontal shredders are suitable for shredding cardboard, paper and cardboard. With a shaft shredder you process plastics, mixed waste and also metal. There is even special shredding technology for banknotes, e-waste and data carriers. These solutions take into account the high data security standards that must be observed when destroying such objects.
The transport of waste within the extraction plant
The transport of waste is an important function within the extraction system. The aim is to remove the residual materials from the production or packaging area as quickly and automatically as possible. Various techniques can be used for this purpose. If possible, pneumatic conveying with negative pressure is used.
This technique offers decisive advantages, particularly in the case of dusty air. It prevents contaminated air from escaping from the lines. This is ensured by the vacuum that prevails in the pipes. At the same time, a vacuum system makes it possible to implement particularly compact solutions. Thanks to a high transport speed, these nevertheless offer high and very reliable performance.
Compaction, compression and preparation for final disposal

After the residual materials, dust and waste have been separated and crushed, the last work step takes place in the extraction plant. Before the materials are ready for disposal, they are compacted. This is done, for example, with balers or compactors – depending on what type of waste is being compacted.
The balers compress the waste to a minimum level. Standardized compression in bale form also makes further processing much easier. In this way, the volume can be reduced by a factor of twenty in some cases. The square shape then also makes transport and storage of this waste much easier. This often results in a raw material that returns to the recyclable material cycle.
Individual solutions for many applications
Extraction systems adapt to the environment and the type of waste. The list of residual waste and waste materials that the systems can handle is very long. This is achieved by individual components within the system. This allows for a customized setup based on your on-site conditions. An extraction system can handle the following waste products, among others:
- gray cardboard
- corrugated cardboard
- paper
- banknotes and security documents
- fust and similar fine particles
- plastics of various classes
- stampings from production
- foils
- metals and aluminum
- flexible packaging
- dust of various types
- gaseous pollutants
Extraction systems from Hunkeler Systeme AG
We at Hunkeler Systeme AG offer you a wide range of extraction systems for waste. These differ in size and performance class as well as the characteristics. So you will find suitable plants for trade or commerce, as well as for large-scale industry and production.
Control and automation: How to simplify waste disposal processes
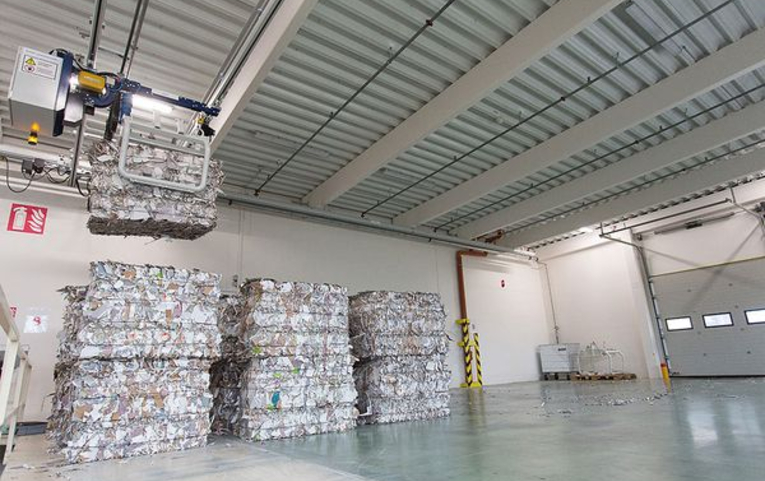
A significant advantage of a system for waste disposal with a central extraction unit is the high degree of automation. An optimum condition is reached when the complete process from extraction to final disposal runs without manual intervention. This can be achieved with our extraction systems.
Waste and residual materials from packaging or production are continuously extracted by the system. Separation and air filtration also take place completely automatically. The entire transport in all phases is achieved via pneumatic conveying in negative pressure until the materials arrive at the presses. These systems also operate fully automatically. Suitable manual solutions are available for the different materials, such as roller compactors, drum presses, or horizontal presses.
Automatic processing and depositing is also possible after pressing. For this purpose, Hunkeler offers bale stacking systems. These take over the transport of the pressed bales to the designated storage location. Stacking on pallets is thus possible. Other waste goes directly into press containers, where the unit automatically compresses it.
Even after the waste is in the container awaiting removal, automation can be achieved with the help of modern technology. By connecting with smart sensors and IoT, the compacting container itself calls the waste disposers as soon as it is full.
Hunkeler’s intelligent solutions ensure that the system works automatically as far as possible in the individual phases of waste disposal. On the one hand, this increases the speed with which residual waste is removed. On the other hand, it optimizes waste disposal processes. This reduces manual labor and thus efficiently cuts costs in your company.
Automatic filter units for air space cleaning
An important part of the extraction system are the filter units. Hunkeler offers solutions of different sizes. For example, the HJF series includes filters with volume flow rates between 8000 and 50,000 cubic meters per hour. Individual solutions between up to 100’000 cubic meters are also possible.
The negative pressure system makes it possible to use pipes with a particularly thin diameter. This saves space above all. In addition, this technology often makes it possible to integrate the filter systems directly into the process line. Our filter units operate efficiently and quietly. In combination with a noise control system, it is possible to keep the noise level below 70 dB.
The systems can be equipped with different filters. These include fine filters and activated carbon filters. Thus, the filter systems are prepared for different types of impurities. These can be solids, particularly fine dust or gaseous contaminants. Automatic differential pressure measurement makes it possible to test the cleaning power of the filters during operation and to actively monitor filter performance.
Hunkeler automatic filter monitoring ensures safety and clean air
A component for automatic monitoring of the filtering process can be integrated into the extraction systems. This electronic system continuously measures the dust content in the filtered air. If the values are too high, the system stops, thus guaranteeing 100% control.
Thanks to the summer-winter circuit, it is possible to discharge the filtered exhaust air either to the outside or back into the operating rooms. The different high-performance filters as well as the automatic monitoring guarantee the functionality as well as clean air at any time. This ensures high air quality in the operating areas, which is also important for the health of the employees.
Energy-efficient and economical: Ecological aspects of extraction systems
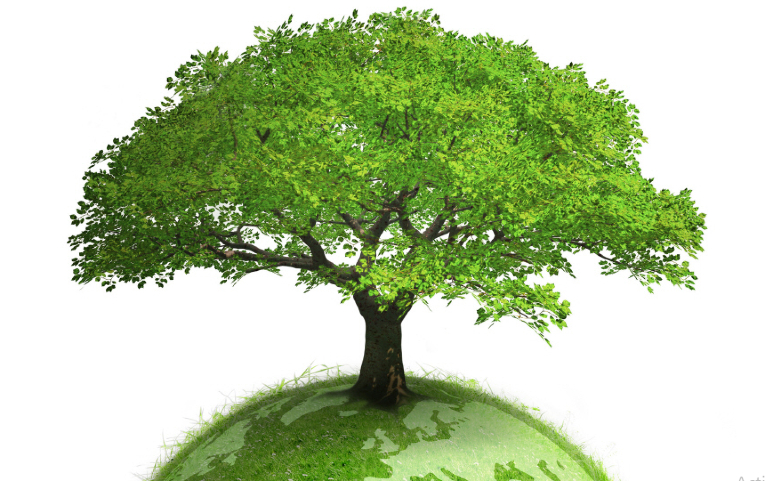
Nowadays, topics such as energy efficiency and ecological footprint are very important for companies and consumers alike. Customers expect companies to handle resources sustainably. At the same time, rising energy and raw material prices ensure that companies also think about sustainability out of their own interest.
With extraction systems from Hunkeler, you cover all aspects in this area. First, you ensure a closed raw material cycle by separating and collecting residual materials. You can often feed the collected waste materials into the recyclable materials cycle. In addition, the systems from Hunkeler convince with their intelligent solutions for energy saving.
We at Hunkeler Systeme AG have developed the Greenline Concept for our extraction systems. This is a series of technologies that reduce energy consumption. For example, the system features the ASA automatic shutdown system. This controls the individual components of the system individually and deactivates them as required. The automatic shutdown system can also be retrofitted.
The ESS energy-saving system regulates the output of the extraction system according to the workload. This makes it possible to run the system only at the necessary load. In the case of fans, this ensures potential savings of up to 60 percent. At the same time, this reduces wear on the system, which in turn benefits service life.
In addition, waste heat recovery is possible with Hunkeler’s extraction and compression systems. This is accomplished by circulating the filtered air that the system does not exhaust from the building. In this way, you reduce heating and cooling costs in different seasons and further optimize energy consumption.
The advantages of Hunkeler extraction systems
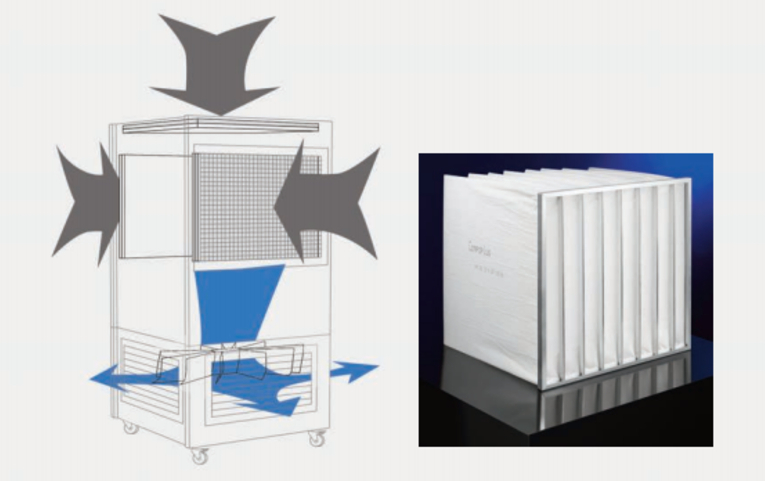
Our extraction systems are characterized by their compact design, energy-efficient operation and versatile individual adaptation options. Also, among the advantages of our extraction systems are the options for room air filtration. With such a system, you create an automatic system for waste processing and improve the indoor air quality in your plant. These are the main advantages of our extraction systems:
- direct integration into the production
- space-saving due to negative pressure technology
- cleans the air in the packaging and production area
- allows the automation of disposal processes
- presses and crushes waste for easier disposal and storage
- saves energy through intelligent controls
- increases the speed of processes and production machines
Are you interested in a powerful and reliable extraction system? Then contact us now. We look forward to your inquiry and will work with you to find solutions that are ideally suited to your operation.