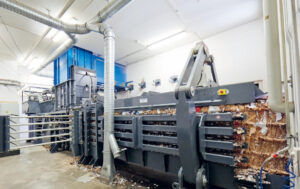
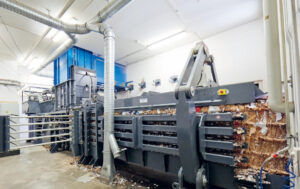
Balers for higher yields with recyclables
Working with recyclable materials such as paper, cardboard or plastics plays a central role in waste disposal logistics. Baling presses are an efficient way to prepare the valuable raw materials for transport and further processing. Modern systems not only shape the material into a space-saving and easy-to-handle form. They also operate much more energy-efficiently than older systems.
What are the balers?
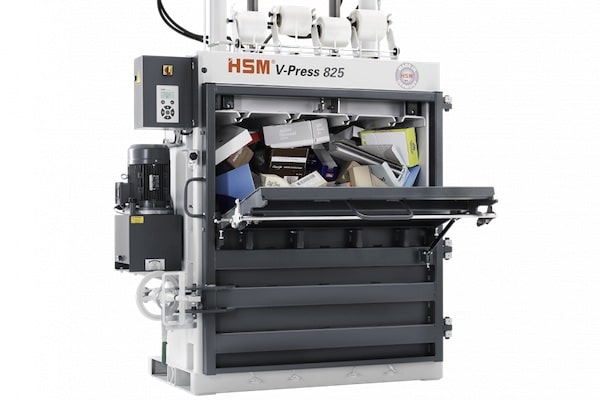
A basic distinction is made between vertical balers and horizontal balers. Horizontal systems typically have a higher processing capacity than vertical ones and operate fully automatically. They are particularly suitable for use in industrial plants and recycling companies and can be integrated into fully automatic complete systems if required. Vertical presses, on the other hand, are space-saving and easy to operate and can be used in a wide variety of plants.
Baling presses are used for the compaction of various recyclable materials. In addition to paper and cardboard, for example, also for PET, PE plastics and films.
How do companies use Hunkeler Systeme balers in practice?
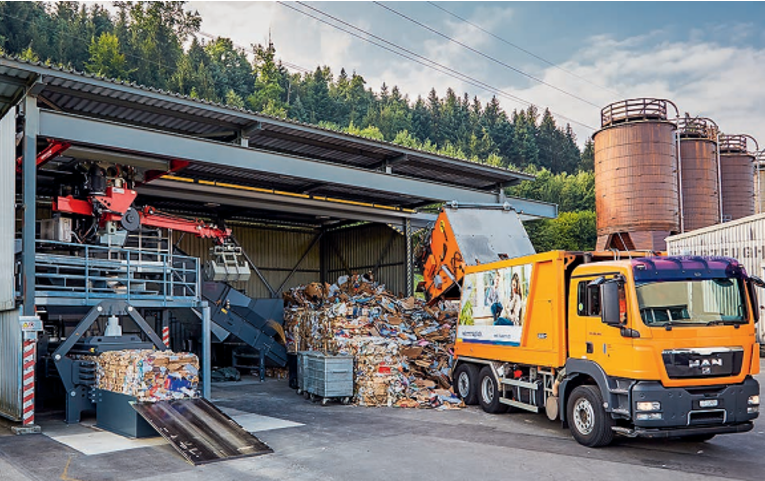
The example of the waste and recycling Centre Ibach near Lucerne shows how companies and waste disposal operations work successfully with balers. The municipal depot works with a new baler from Hunkeler Systeme and compacts cardboard waste collected in Lucerne. With an output of up to eight tons per hour, the system is around 50 percent more efficient than its predecessor.
For the waste and recycling Centre, the decisive factor in the purchase was above all efficiency in ongoing operation. Important factors for this were, among others:
- Control system with focus on energy efficiency
- Turnkey complete system from a single source
- High processing capacity
- Hunkeler systems as a permanently reliable service partner
Department head Heinz Zurkirchen was also satisfied with the cooperation during the installation of the plant. “The project management communicated well, and the installers worked expeditiously,” he reports.
He and his team were particularly impressed by the baler’s intelligent control system. The frequency-controlled drive of the baler is automatically switched off when no compaction is taking place. Nevertheless, the system is available in standby mode at all times, so that the plant reacts quickly. Bottlenecks in operation are thus effectively avoided.
In the first two months of operation alone, the new baler processed and compacted around 400 tons of cardboard waste. This corresponds to around 20 percent of the annual volume at the Ibach site. The plant is dimensioned in such a way that even above-average quantities of material can be processed without any problems at short notice. The bales, which are uniform and compact, can thus be delivered quickly and efficiently to partners in the recycling industry.
Do you have any further questions about our balers or our company? We look forward to getting to know you. Get in touch with us! We will be happy to explain the advantages of our large range of baling presses to you in an individual consultation.